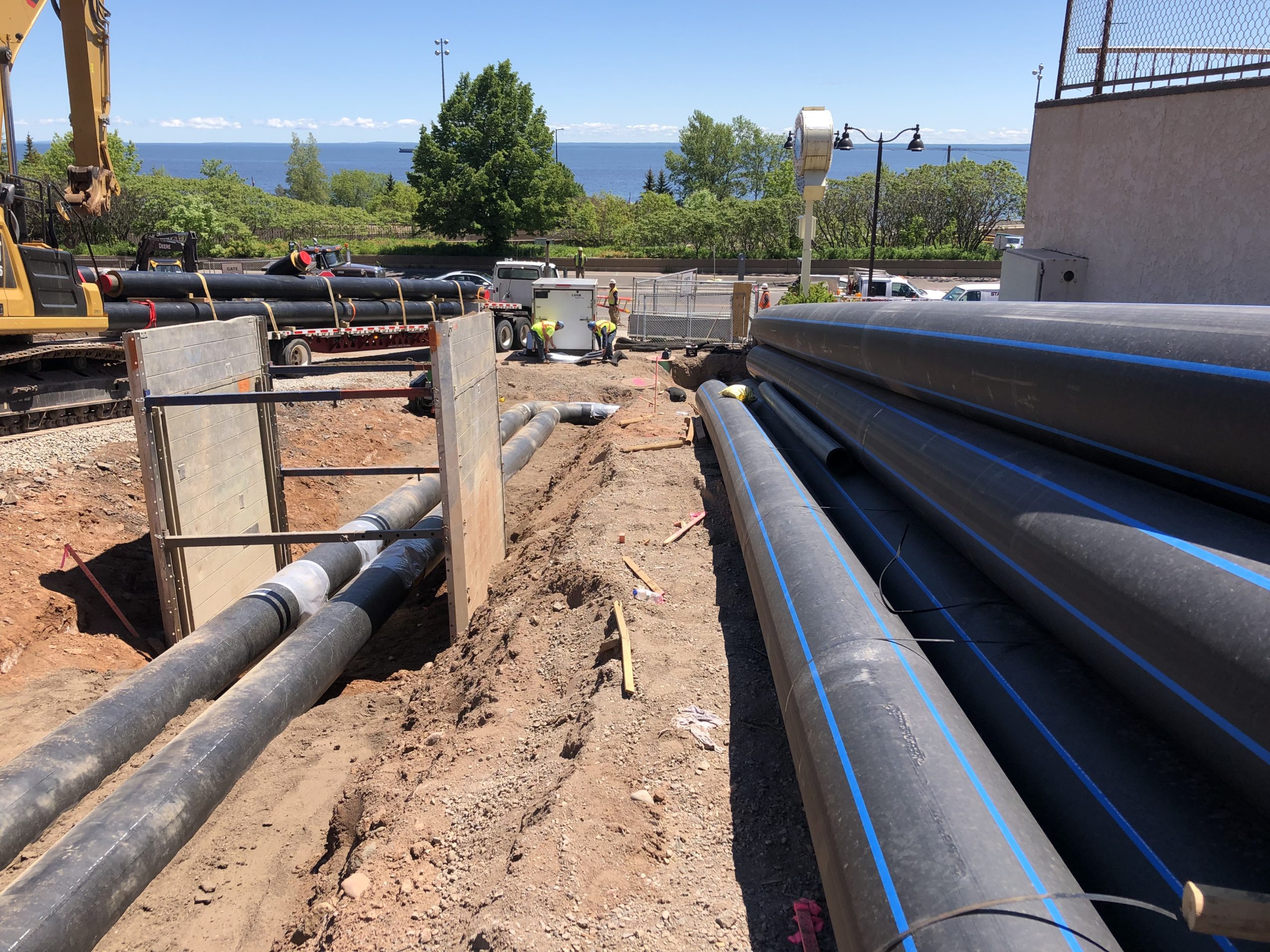
Far Superior: Serious efficiency gains in Duluth business and hospital corridors
December 23, 2020 by Ever-Green Energy
2020 marks the close of a three-year transformation project at Duluth Energy Systems. Since stepping in as operations manager for the City of Duluth in 2012, Ever-Green Energy has remained steadfast in delivering system improvements and carbon reductions that meet the City of Duluth’s long-term vision for climate-resilience and cost effectiveness.
Beginning in 2015, the City of Duluth leveraged its planned Superior Street reconstruction to modernize its energy system at the same time, upgrading from steam to hot water distribution. Updating this energy infrastructure provides Duluth with a pathway to reduce the energy demands of the system and in customer buildings, providing opportunities for fuel flexibility, financial savings, and carbon reduction. This project entails transitioning 11 blocks of distribution piping and converting 27 customer buildings to hot water service.
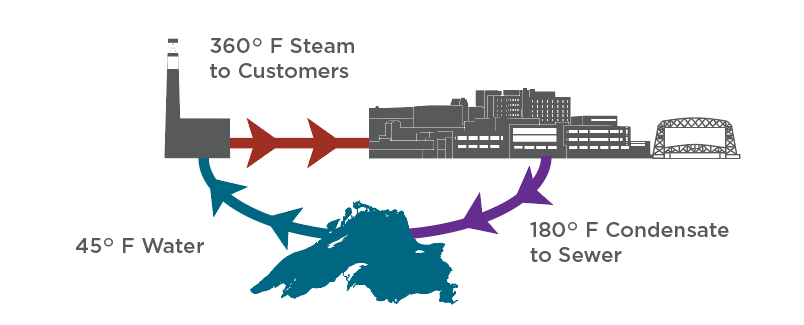
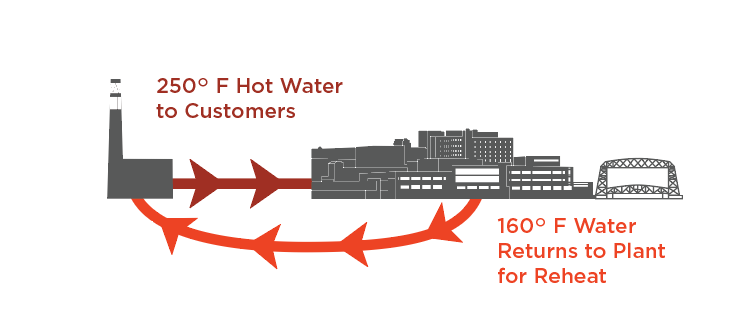
We sat down with general manager, Terry Nanti, and senior program manager, Sean McFarling, to discuss projects and outcomes that have shaped the work in 2020.
How do the accomplishments of 2020 fit into the overall Superior Street project?
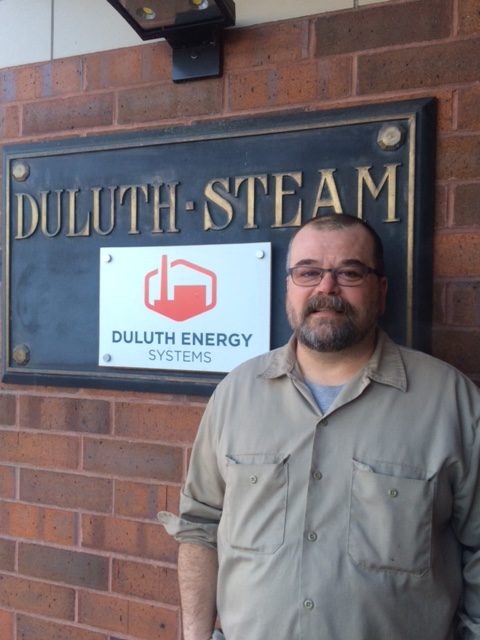
Terry: The Superior Street project was scheduled for three years to install the infrastructure, not only for our project but for other City projects. Duluth Energy Systems and Ever-Green chose to make the building conversion project a four-year construction cycle based on the size and complexity of the buildings being converted in the third phase.
Phase 3, which took place this year, included the plant connection and the buildings on the north side of Superior Street, which is a lot of work to do in a short period of time with a finite end date of when it starts to get cold in Duluth. We will convert the south side of Superior Street during the spring and summer of 2021. The project will be fully functional for the 2021 heating season.
Sean: The distribution system transitioning from steam to hot water is a critical step for system improvement. There will be less waste heat in the streets and in most instances the community won’t even realize the system is there. The lower pressure and lower temperatures of the hot water loop result in increased safety and energy efficiency too.
What have the changes on Superior Street required at the plant?
Terry: The plant conversion is what ties everything together. We’ve built the hot water network over the course of the last three years. Up until this point, we’ve been generating hot water at a remote customer site because the entire system hasn’t been connected. When we get the plant fully converted in January 2021, we’ll be generating hot water in the plant. The steam will go from the boiler into the hot water converting station, and the hot water will be pumped out of the central plant to the network. We will greatly increase efficiency by closing the distribution loop.
That means the water used for heating the buildings will be returned to the plant, reheated, and sent back out to the system. Significant energy is saved here, as we are only heating water back up about 50 degrees versus the open loop steam system. In an open loop steam system water is continuously heated from roughly 40 degrees to 365 degrees to be distributed to the system, and that energy is never returned back to the plant. In addition to saving energy, we also conserve a significant amount of water, resulting in additional benefits to the overall project.
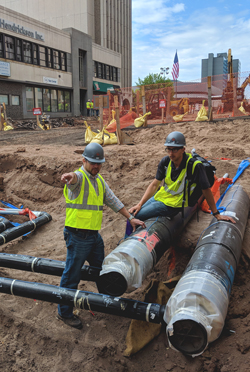
There is significant energy savings there: water reduction, chemical treatment reduction, and associated cost reduction. The plant has been operating since 1932, and this is the largest internal plant project that’s been undertaken since it was built. The plant now has new equipment and controls and a highly efficient way to generate the hot water.
To reduce the City’s carbon footprint, we’ve used different process control schemes to gain more efficiency on the boilers and increase the amount of time that we can burn natural gas, so that’s had a big impact on efficiency and carbon reduction. When you compare the plant’s 2020 coal usage with 2010 usage, we burn 1/10 of the coal that we used to burn, and that’s because of projects in the plant like the gas burner conversion, the hot water conversion on Superior Street, and process control improvements.
The plant has come a long way, and over the next couple of years as the hot water system grows and efficiencies are gained, we hope to eliminate that remaining coal altogether. We’re also exploring renewable fuels in the next few years. Fuel flexibility and reducing the energy we produce also helps.
Sean: The hot water distribution system consistently holds 11,000 gallons of water. It was a feat to fit all the equipment, piping, and structural supports that were necessary in the plant to house equipment for all the water that will be in the system. That was a significant challenge and resulted in a lot of problem solving. There were some unknowns that we uncovered through the process, but for a system of this scale to be able to provide hot water off of the steam system efficiently is impressive, and I give a lot of credit to our engineers and our contractors who worked on this project. We’re looking to complete work on the plant conversion by December 2020 and have the system operational in January 2021.
What has this meant for Duluth Energy Systems customers and the City of Duluth?
Terry: Duluth Energy Systems customers who were converted had a state-of-the-art heating system installed in their building. They are seeing simpler interfaces in their buildings and more hands-off operation of their building equipment. They’ll have significant efficiencies attributed to that. The customers who converted over the past two phases are seeing a 25% reduction in energy consumption. It’s a money saver for them and hot water is a much better heat medium because it’s much easier to control than steam, so those buildings have gained comfort as well.

For the customers that remained on steam and weren’t able to convert to hot water due to their building system or weren’t on the list based on location, the changes make the plant more efficient, so they gain the benefits of that efficiency, which results in rate control for those customers. As we lose less heat through the distribution network because hot water is so much more efficient than steam, we consume less energy and that results in a lower energy rate for the steam customers as well.
For the City, this work has meant modernizing a City asset and increasing resilience and redundancy. It also has significant implications for greenhouse gas emissions. As we become more efficient, we consume less fuel and power, which helps the City further their carbon reduction goals.
What has led to your success in ensuring safety during this pandemic?
Terry: Committing to and following safety protocols and continuing to have conversations within our team and with our contractors has really contributed to safe outcomes.
As the pandemic stretches out month after month, it could have resulted in team members letting their guard down, but the simple reminder that getting the virus in our plant will affect our families and community members because it affects the medical district was impactful. Having our team stress that to contractors on-site has kept people performing at a high level and being diligent about protecting themselves and others.
How has the project improved system efficiency?
Terry: I think that the hot water system will have the biggest impact on efficiency. We’ve already seen a decrease in our losses over miles of our distribution network after replacing blocks of steam pipe with hot water pipes. An earlier project that’s had an impact on efficiency was upgrading our gas burner management system on two of our boilers in 2016.

Sean: The only thing I would add on efficiency is the overall transformation to the closed-loop system. There’s no longer that constant temperature makeup that needs to happen to go from lake temperature to steam because we are now returning the warm water to the plant and capturing condensate to be reheated and sent back to customer buildings.
What is the City of Duluth’s role?
Terry: The City is absolutely a partner of ours on this project. Not only do they own the system, but they care about advancing the system. That care led to the plant conversion and the Superior Street project. They see the district energy system as a long-term asset that is integral to the business community in downtown Duluth. The system really helps support the environmental position that the administration is so serious about. Mayor Larson and her team care about reducing carbon and what better way to do that than to have a district energy system where you can make a change to the system and affect 160 customers.
Sean: I would absolutely second that. Without the City’s support and insistence on reducing carbon, setting realistic goals, and making district energy a central part of that I don’t think any of this happens.
We see other cities with district systems that don’t prioritize carbon reduction as significantly or don’t take climate change as seriously, and you just don’t see decarbonization transitions happening in those systems. They seem to stay stuck where they are because it takes an upfront investment to retrofit or advance these systems, but if you don’t value that carbon reduction and see district energy as a central part of that, it doesn’t move forward.
Without the City of Duluth’s insistence on striving toward these goals and seeing Duluth Energy Systems as a central part of that, this project doesn’t happen.
What projects and improvements are in store for 2021?
Sean: In 2020, we began our work to connect the Essentia Health, Vision Northland, and Regional Exchange District integration to the system. The growth there is important to the city and the region and we had the opportunity to create hot water connections to the Essentia Health campus and extend hot water pipe to St. Luke’s Hospital campus.

We also completed tunnel renovations under I35, reconstructing both end walls of the tunnel, reinforcing the inside supports of the tunnel, and modifying the tunnel to fit the hot water pipes. We were able to renovate the steam line components to be able to fit the hot water pipes and cross I35 without having to dig it up. This makes the connection to send hot water out from the plant through the distribution network to Superior Street and the hospital district.
We have to make the final connection between the Superior Street and the Essentia Health project to St. Luke’s Hospital with both the hot water and the reconstructed steam lines, which will be completed in the fall of 2021. That’s going to be a very significant project in and of itself to finish those last six blocks of piping. On Superior Street, 2021 is really about connecting the remaining customers.

Terry: When phase 3 customers on Superior Street are added and the medical district is completely connected, we will be adjusting to the load increase. For our team in Duluth, 2021 is a transition year at the plant as we familiarize our team with the new system and controls and learn how to run it at peak efficiency.
What are you most proud of in the work this year?
Terry: I am most proud of the fact that the work got done on budget and on time with no injuries to the people involved in the project in the midst of a pandemic.
Sean: I would absolutely agree with that and especially highlight the lack of COVID-19 exposure and how all that was managed. Being able to complete all these projects with no lost time for our team is really quite a feat during a pandemic. It’s also really rewarding now to have the hot water system completely tied into Superior Street.
For me personally, that’s something that I’m pretty proud of because that’s where my involvement started, and most of my time early on was spent in the design of the hot water system and hot water pipes and now to see that fully come to completion is pretty satisfying.
Learn more about Ever-Green’s work at Duluth Energy Systems in the utility operations profile.
Thank you to all of our partners who contribute to the success of this work.
Engineering Consultants:
- American Engineering Testing (AET)
- Arrowhead Consulting & Testing
- Braun Intertec
- Hammel Green and Abrahamson (HGA)
- LHB
- Meyer Borgman & Johnson (MBJ)
- System Technology Services (STS)
- TKDA
Contractors:
- Carlson Brothers
- Carlson Duluth
- Corval Constructors
- Egan Company
- Jamar Construction
- Northern Horizons
- Northern Industrial Insulation
- Northland Constructors
- Pioneer Power
- Stack Brothers Mechanical & Electrical
- US Siteworks
- Lakes States Insulation
- Accuren Testing
- Infinity Access (scaffolding erector)
- ACCT (asbestos abatement)
- AW Keuttel & Sons (roofing contractor)
- Sunbelt Rentals and United Rentals
- Viant Crane Service
- Kraemer Crane Service
- Atlas Foundation Company
- HMI Duluth
Equipment Suppliers:
- Energetx
- Logstor
- Campbell-Sevey
- Parsons
- Hunt Electrical
- Belknap Electrical
- Duluth Electrical Contractors